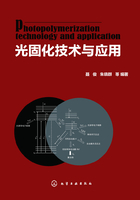
第二节 光固化技术在平版印刷油墨中的应用
平版印刷又称为胶印,是在印刷领域中应用最广泛的一种印刷方法。平版印版的图文部分与非图文部分基本在一个平面上,图文部分亲油疏水,非图文部分亲水疏油。平版印刷大部分是利用油水不相溶原理来完成印刷的。印刷时先给印版供水(实际为润湿液,也称为润版液),非图文因其亲水而被水覆盖,图文部分因其疏水而不能得到水,然后再给印版供墨。由于非图文部分表面已有水,油墨只能传递到图文部分,通常印版图文部分的油墨先转移到橡皮布滚筒上,然后再转移到承印材料上,属于间接印刷,也是胶印名称的来源,采用UV油墨的胶印如图5.1所示。也有一些平版印刷在印刷过程中不需要水的参与,这是因为所用印版的非图文部分表面是斥油的,印刷时只需要给印版供墨即可,这种印刷方式也称为无水胶印。

图5.1 UV胶印示意图
一、UV胶印油墨
在胶印过程中采用UV油墨,具有以下优势:
①印刷质量优良。UV胶印油墨印后立即固化干燥,油墨不渗入承印材料内,故色彩更鲜艳,大大提高了印刷品的色彩饱和度,并且油墨铺展小,使得网点扩大小,清晰度更高,印刷品色调再现性好,非常适合精细产品的印刷。此外,采用UV胶印油墨印刷的产品具有耐摩擦、耐化学性等高耐抗性,且印品表面整饰效果好,色泽饱满,具有普通胶印油墨无法比拟的优势,特别适合于包装印刷。
②绿色环保。UV油墨在印刷过程中几乎没有挥发性有机物(VOCs)的排放,解决了油墨干燥过程中的环境污染问题。同时,印刷品在到达收纸部分已经固化,可以免去普通油墨印刷品在收纸部分的喷粉环节,既利于印刷环境的清洁,保护操作人员的健康,又避免了由于喷粉而给印后加工所带来的麻烦,如对上光、覆膜效果的影响,还可进行连续后加工。不仅改善了作业环境,而且提高了生产效率,缩短了交货时间。另外,紫外线固化设备能使UV油墨低温下快速固化,它的能耗比普通油墨印刷通过热风或红外烘干的方式进行干燥所消耗的能量低得多,可节省大量的能源。
③改进了印刷工艺。UV油墨经UV光源照射才固化,照射前在墨罐中不结皮,在印机或版上也不会干结。因此,胶印机停机不用清洗墨辊和印版,解决了胶印机停机的后顾之忧,减少了油墨的浪费,节省了清洗时间。
④使胶印适用于多种承印材料,拓宽了胶印的应用范围。采用UV胶印油墨使得胶印从主要印刷纸张,拓宽到复合纸材料类、金属、塑料等承印材料。这些材料用普通油墨印刷普遍存在干燥慢、附着力小、耐摩擦性差等问题。UV油墨在紫外光照射下可快速固化,且干燥装置体积非常小,可摆脱庞大的干燥装置,同时也替代了溶剂型油墨,避免油墨对环境造成污染。同时,UV油墨在UV光的照射下,发生交联聚合反应,相互交联形成网状结构,极大地提高了墨层表面的物理性能,从根本上解决了附着力和耐摩擦性等问题。
⑤扩大了胶印在特殊印刷领域的应用。随着UV胶印油墨的应用,许多厂家利用它进行一些特殊产品的印刷,如光栅立体印刷,从而使得立体印刷可以大批量地进行生产,而且产品的质量得到进一步提高,进而拓宽了胶印在特殊印刷领域的应用。
由于UV胶印油墨的使用提升了印刷质量,并拓宽了胶印应用范围,随着包装印刷的高速发展,UV胶印油墨得到了越来越广泛的使用。UV胶印油墨的品种很多,根据所印刷的承印材料种类以及印刷用途,主要有UV胶印纸张油墨、UV胶印合成纸油墨、UV胶印镀铝纸油墨、UV胶印塑料油墨、UV胶印金属油墨、UV荧光防伪胶印油墨等。
由于平版印刷的图文部分和空白部分在一个平面,所以印刷墨层很薄,一般单色墨层厚度在1~2μm左右,是所有印刷方式中较低的,有利于光固化的进行。但是,墨层太薄,会对颜色表现力不利,因此要提高颜料含量,一般为15%~21%。白墨和黑墨颜料含量更高,这提高了光固化难度。同时,胶印速度较快,一般在100~400m/min,这对UV油墨的固化速度提出了较高要求。由于胶印为长墨路印刷体系,所以黏度较高,一般在200Pa·s左右。由于胶印在印刷过程中有水的参与,因此要求UV胶印油墨有很好的抗水性能,从而达到理想的水墨平衡状态。
根据对油墨固化速度的要求,UV胶印油墨在设计时一般选用固化速率快、官能度高的丙烯酸树脂。UV胶印油墨的光引发剂用量比较大,一般在6%以上。为了提高表面固化速率,还要加入少量叔胺。
在实际印刷过程中,UV胶印油墨对水量的宽容度小,水墨平衡难控制,难以达到传统胶印油墨的印刷适性。导致UV胶印油墨的水墨平衡性能差的原因主要有以下两方面:首先是UV胶印油墨中所使用的丙烯酸酯低聚物和活性稀释剂,通常带有羟基、氨基等高极性基团,对润版液具有较强的亲和性,与极性小的油性连接料相比,前者的乳化可能性更大;其次是UV胶印油墨的印刷基材主要是以合成纸、金银卡纸和塑料等非吸收性材料为主,对润版液的吸收性差,这给印刷中水墨平衡又增加了更多可变因素。经验表明,使用残留羟基多和极性大的反应性低聚物(含调节用树脂、活性稀释剂、助剂)时,必须十分慎重。主体低聚物的选择是改善UV胶印油墨的水墨平衡性能的关键。环氧丙烯酸和聚氨酯丙烯酸酯预聚物的分子链上含有羟基、氨基等官能团,具有较强的亲水性,但损失了油墨的抗水性,所以从改善油墨的水墨平衡性能角度来看,聚酯丙烯酸酯具有更好的抗水性,是最佳的选择。目前,从油墨性能方面看,UV胶印油墨体系大多以聚酯丙烯酸作为主体树脂,改善油墨的水墨平衡性能也是主要选择依据之一。但是聚酯丙烯酸酯低聚物在硬度、耐摩擦性和溶剂抗性方面还有待进一步改进。另外,在保持油墨体系黏性相近的条件下,采用更高分子量的丙烯酸酯低聚物,可以提高油墨的抗乳化性能,但这是在高分子量树脂在油墨的配方中达到一定的比例时才可以,可能是由于高分子树脂之间通过相互缠结,形成了更大的物理网状结构,有效阻碍了水分子向油体系内部渗透,从而改善了油墨的乳化性能。然而,丙烯酸酯低聚物的高分子量化是以降低官能度、损失固化速度为代价的。这就需要在设计油墨配方时进行综合考虑,避免为改善油墨的水墨平衡性能,而导致其他性能变差的不良后果。环氧丙烯酸酯类低聚物是影响油墨乳化率的主要因素。因此,在保证固化速度和油墨黏度的前提下,应控制环氧丙烯酸酯类低聚物的用量,使UV胶印油墨能保持较强的斥水性,以保证在实际印制生产中具有良好的印刷适性。
UV胶印油的连接料主要由较高极性的低聚物和活性稀释剂组成,应用于UV胶印油墨中的颜料大多为极性较低的有机颜料,这些高极性的低聚物体系对低极性的有机颜料粒子表面的亲和性是比较差的,难以提供良好的颜料润湿性。同时,UV胶印油墨连接料所使用的主体丙烯酸酯低聚物分子量较低,通常为1000~2000(而传统胶印油墨所使用的松香改性酚醛树脂分子量为20000~50000)。总之,与传统胶印油墨相比,UV胶印油墨的树脂和连接料体系具有低分子量、高极性的特征,不能提供令人满意的颜料润湿性和分散稳定性。为改善UV胶印油墨的颜料润湿性和分散性,提高生产效率,首先要选择合适的主体低聚物树脂。脂肪酸改性丙烯酸酯低聚物因具有较高的分子量、低极性而具有良好的颜料润湿性,特别适合颜料含量较高的胶印油墨体系。但由于部分丙烯酸官能团被脂肪酸所取代,脂肪酸改性丙烯酸的反应活性差、Tg低,会影响油墨的固化速率和墨膜的物理性能,通常必须和低黏度、高官能度的低聚物配合使用。选择合适的颜料也是改善油墨分散性能的有效途径之一,但是除UV油墨专用炭黑以外,极少有专门与UV胶印油最配套使用的有机颜料,有机颜料的最终确定只能依靠大量的实验来进行。不过UV体系颜料选择有一个原则,就是在UV胶印油墨中适用的颜料应该是具有一定极性的。
UV胶印油墨和传统胶印油墨相比在流变性能方面存在显著差异。首先,丙烯酸酯低聚物的颜料润湿性差,使UV胶印油墨在低剪切速度下表现出更强的结构,并对油墨在印刷机的墨槽中的流动产生不利影响;其次,丙烯酸酯低聚物具有特殊流变性能和低分子量的特征,导致UV胶印油墨内聚力差,对温度变化敏感,表现出高黏性、低黏度和丝头长的特征,在高速印刷条件下,由于油墨体系的黏弹性不足,容易出现飞墨现象,如果为了顾全油墨的流动性和分散性而选用易分散或高流动性的颜料,则此类问题会更加突出。目前大多采用添加非反应型助剂的方法来改善体系的抗流变性能,以提高UV胶印油墨抗飞墨性能。通常在油墨配方中加气相SiO2、滑石粉、有机膨润土和有机硅树脂等具有一定增稠作用、可提高触变性的填充料,通过增加体系的内聚力和黏弹性来防止飞墨,但这些助剂的效果很有限,无法从根本上解决问题,而且会对油墨的光泽度、附着力等性能产生不良影响,改善低聚物树脂自身的流变性能是解决UV胶印油墨流变问题最有效的办法。从理论上看,在油墨配方中引入100%反应活性、具有流变性控制效果的低聚物树脂,不但能改善油墨的印刷适性,而且还可改善油墨的最终固化成膜性能。
由于UV胶印油墨有瞬间固化和低温固化的特性,不仅在普通的纸张上可以使用,还可以应用于合成纸、金属覆膜纸、塑料等各种非吸收性承印材料。然而,在自由基聚合时,单体或低聚物间由固化前的范德华力作用的距离变为固化后的共价键作用的距离,两者之间距离缩小,因此体积收缩明显。加之固化时间极短,墨层的内部残存着很大的应力,因此与一般的溶剂型油墨相比,UV胶印墨有附着力变差的趋势。目前,UV胶印油墨在一些特殊的塑料基材(如PE、PP和部分PET)上不能提供良好的附着力,这主要是由于这类材料具有活性稀释剂无法溶胀、表面极性低的特征,已固化墨膜与基材之间无法形成有效的作用力,导致附着力差。解决UV胶印油墨对这些塑料的附着问题是行业中难以克服的技术难题,根据实践经验,解决UV胶印油墨对这些基材的附着问题,通常从以下几方面着手:①增加低表面张力的活性稀释剂,改善油墨对基材的润湿性。②选用低官能度的活性稀释剂和低聚物,以减小油墨的应力和体积收缩。③选择高分子量、低Tg的低聚物。④使用特殊官能团改性的低聚物,例如氯化聚酯丙烯酸酯等。⑤添加附着力促进剂。但是这样处理往往会导致油墨的固化性能、印刷适性有变差的趋势。从应用状况来看,要使UV胶印油墨对所有基材都具有良好的附着性能是很难的,所以在改进油墨性能的同时,也必须对基材进行表面预处理(如电晕处理、火焰处理等)或先涂布增黏底涂层等,以改善基材的表面性能。总之,必须结合印刷工艺共同解决UV胶印油对基材附着困难的问题。
使用UV胶印油墨还需注意下列问题:①印版,胶印使用的阳图型PS版或CTP印版,其图文部分都是光或热分解型材料,这些材料会被UV油墨中活性稀释剂和光引发剂分解,造成印版耐印力下降,故必须使用UV油墨专用的阳图型印版。如果用一般的阳图型PS版,需要进行烤版处理,即按照常规方法晒制的普通PS版,需要在250℃左右的温度下烤版10~15min,CTP版也需要烤版10~15min。②胶辊、橡皮布,UV油墨中的活性稀释剂会在印刷过程中对普通胶辊和橡皮布进行浸透,一方面造成油墨中活性稀释剂的减少,破坏了油墨的流动性;另一方面造成对胶辊和橡皮布的腐蚀,短期会导致胶辊和橡皮布表面膨胀变形及表面玻璃化,长期印刷时胶辊和橡皮布表面会局部脱皮或产生裂痕。因此采用UV胶印油墨印刷时,需要使用UV油墨专用胶辊,普通油墨和UV油墨兼用型胶辊效果也可以。选用肖氏硬度在40HS以上,由三元乙丙橡胶(EPDM橡胶)或硅橡胶制成的橡胶辊,可以延长胶辊的使用寿命。橡皮布选用普通油墨用或UV油墨专用的橡皮布都可以,后者在橡皮布混合料中加入抗UV树脂成分,可耐UV照射,橡皮布不易粉化,用于UV油墨印刷时,寿命延长。
二、UV无水胶印油墨
无水胶印是采用不亲墨的硅橡胶表面的印版,印刷时不需要给印版供水,直接给印版供墨,通过胶印的方式来完成油墨的转移。
与传统胶印技术相比,无水胶印由于印刷过程中没有水的介入,所印图像因油墨未被稀释和乳化而更光亮、鲜艳,印品色彩饱和度高,印刷密度高,加之印版是平凹版,油墨压印转移时铺展较小,则网点增大小、还原性好、印迹更清晰,更适合加网线数高的精美图像和高分辨率的精密图文印刷。印刷时无需调节水墨平衡,印前准备时间比传统胶印缩短40%,过版纸消耗降低30%~40%,从一定程度上降低了印刷成本,并提高了生产效率。另外,由于不使用传统胶印润版液等含有挥发性溶剂的化学药剂,不向空气中排放挥发性有机物,减少了环境污染,利于环境保护。因此无水胶印具有印刷效果优异、印刷效率高及环保等优点。
UV无水胶印油墨结合了无水胶印和UV油墨的优势,能获得更高品质的印品,印刷效率更高,使印刷更加环保,且可选择更为广泛的承印物。UV无水胶印油墨除了可用于常规印刷以外,在光盘印刷中使用也非常广泛,还被应用于层压金属箔的聚丙烯或者聚乙烯等承印物印刷制作不干胶标签等。
UV无水胶印油墨的基本成分与UV胶印的油墨相似,但印刷中没有水的参与,同时需要与硅胶层有很强的排斥性,因此UV无水胶印油墨有以下特殊的性能要求。①UV无水胶印油墨需要有比普通UV胶印油墨更高的黏度和黏性,这样才有可能提供比较大的油墨内聚力,足以大于油墨和硅胶层之间的作用力,使硅胶层表现为疏油性,使得油墨与非图文部分的硅橡胶层相斥,从而实现无水印刷。同时,由于印刷过程中印版的图文部分边缘没有水对油墨产生阻挡,高黏度的油墨可以降低油墨铺展性,保证印刷质量。因此,UV无水胶印油墨在设计时可选用官能度高的预聚物和活性稀释剂,这对于提高油墨的固化速度也有利,同时可添加一定量的填料,以增加油墨的内聚力。②因为UV无水胶印油墨具有高黏度,所以它在墨辊和印版之间的传递比较困难,这就要求油墨要有特别的设计,使其有较好的流变性能。同时,油墨还要具有较高的触变性。通常在油墨配方中加气相SiO2、滑石粉、有机膨润土和有机硅树脂等具有一定增稠作用、可提高触变性的填充料。③由于无水胶印中没有水对印版的降温作用,要求UV无水胶印油墨最好还要有一个比较宽的温度适应范围。