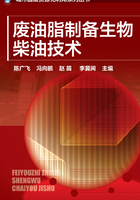
3.2 脱胶
胶质是指磷脂、糖、蛋白质混合物、微量金属及其他杂质。脱胶即是对这些杂质的去除工艺的名称。废油脂脱胶很大程度上影响制备生物柴油的核心反应工艺,若对胶质除去不彻底,这些杂质能导致在反应过程中发生焦化,甚至结焦的现象。脱胶主要有以下几种方式。
3.2.1 水化脱胶
水化利用加热水或稀碱、盐或其他电解质处理废油脂,使废油脂中的磷脂等胶质吸水膨胀,凝聚沉淀而从油中分离出来。水化工艺有间歇式、半连续式和连续式之分。现在一般采用连续式水化工艺,因它处理效果好;缺点是耗汽较多,对离心机维修要求高。该工艺操作简单易行,但只能除去易水化磷脂,大约油料中还有0.2%~0.8%的非水化磷脂,普通水化脱胶后含磷脂为50~70mg/kg,若不能满足工艺要求,需要采用其他方式进行脱胶处理。
水化脱胶工艺流程为:废油脂加热到50~70℃,在静态混合器中与1%~3%的水混合,混合后在水化罐中至少停留30min,以便磷脂在罐中沉淀和凝聚。然后,水化油被输送到分离机。分离机分出粗胶,然后粗胶被泵到废油脂暂存罐或者泵回预处理车间。图3-4为水化脱胶工艺流程。

图3-4 水化脱胶工艺流程
3.2.2 酸炼脱胶
在酸调油中添加1%~2%的水,这样便使多余的酸与沉淀物从油中分离出来。对于高质量棕榈油和动物脂肪,则通常在分离器前的静态混合器中直接混些水就可以了。对于质量低的棕榈油和可可油,酸调与水化过的油必须在凝聚罐中反应20min,才能使有害物质在分离前得到凝聚。
用于预处理油脂的酸炼脱胶工艺是阿伐-拉伐酸脱胶工艺,该工艺同样可用于废油脂的预处理脱胶。该工艺为:将废油脂加热至75~80℃,将废油脂体积总量0.1%体积的85%H3PO4或0.3%的50%柠檬酸(C6H8H7)和油于刀式混合器中混合后,加入废油脂体积总量1%~3%的75~80℃软水,再缓慢搅拌几分钟至1h,然后用离心机分离。工艺流程如图3-5所示。

图3-5 酸炼脱胶工艺流程
3.2.3 特种脱胶工艺
特种脱胶工艺与酸炼脱胶工艺相比具有一个显著的特点是:加添一个部分中和过程,以保证酸性脱胶剂与不可水化磷脂已经形成的配合物不致在高温下发生分解,同时保证磷酸解离完全,使脱胶油磷含量能降到最低限度。
工艺过程大致如下:毛油加热至60~70℃,将磷酸(0.1%废油脂体积总量)与油于刀式混合器中剧烈搅拌30s,然后加入碱液(加入量约为中和磷酸两个质子或柠檬酸三个质子所必需的碱量的70%)。混合物于同温度下用刀式混合器混合。接着加入2%(废油脂体积总量)的75~80℃软水,并缓慢搅拌5~15min,让磷脂凝聚成可分离的絮凝体,然后用离心机分出胶质。脱胶油含磷5~30mg/kg(依毛油质量而定)。再经后道洗涤工序,含磷量可再降低一半。工艺流程如图3-6所示。

图3-6 特种脱胶工艺流程
3.2.4 完全脱胶工艺
该工艺类似于特种脱胶工艺,不同点在于它采用两台离心机分级分离。第一级分出的为贫油油脚,第二级分出的为富油油脚。富油油脚再返回重新处理。该工艺与特种脱胶工艺相比,缺点是增加一台离心机;因油脚返回,处理量降低10%~15%。优点是精炼得率增加0.5%,脱胶油磷含量进一步降低。工艺流程如图3-7所示。

图3-7 完全脱胶工艺流程